Paddy
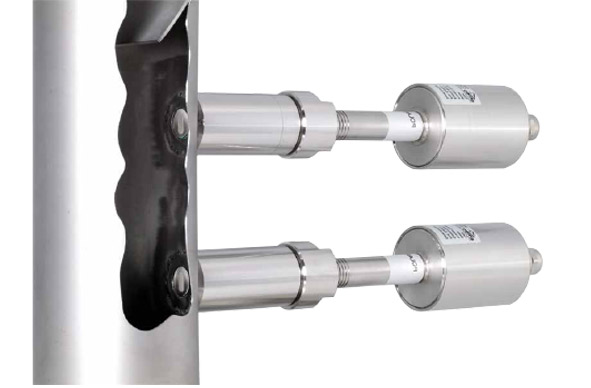
In virtually all processes in which solids are processed, they must be ground and then screened. At the end of these processes there are always at least two fractions: the fine particles, often also referred to as the material flow, and the coarse particles. To date, there has been no easy way to check the material flow for the presence of oversized particles. This unwanted situation often occurs when a so-called screen break occurs. Unless screen breaks are detected at an early stage, large scrap quantities may be produced or it may be necessary to subsequently re-screen large quantities of material. PADDY is a particle sensor that can detect and trigger an alarm in the presence of oversized particles in the material flow. PADDY uses state-of-the-art microwave technology in combination with intelligent evaluation software.
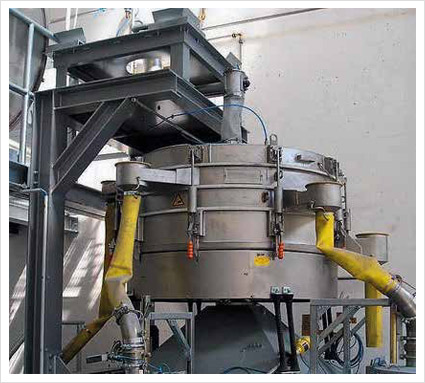
In virtually all processes in which solids are processed,
they must be ground and then screened.
At the end of these processes there are always at least two fractions: the fine particles, often also referred to as the material flow, and the coarse particles. To date, therehas been no easy way to check the material flow for the
presence of oversized particles. This unwanted situation
often occurs when a so-called screen break occurs.
Unless screen breaks are detected at an early stage, large
scrap quantities may be produced or it may be necessary
to subsequently re-screen large quantities of material.
PADDY is a particle sensor that can detect and trigger
an alarm in the presence of oversized particles in the
material flow. PADDY uses state-of-the-art microwave
technology in combination with intelligent evaluation
software.
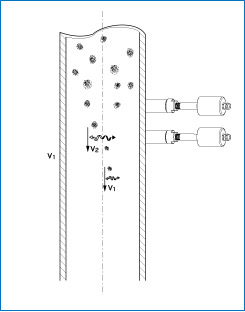
PADDY can be installed in free-fall pipes downstream from
screening or grinding systems. Microwaves with a frequency
of 24.125 GHz are fed into the product stream and backscattered
by the particles. This scattering effect occurs
differently for particles that are significantly smaller than
the wavelength of the emitted microwaves (Rayleigh scattering)
and particles whose size lies in the same wavelength
range as the microwaves (Mie scattering).
Our patented measuring method consists of two microwave
sensors, which are installed in a free-fall pipe.
Due to the arrangement of two baffles, all particles in the
product flow begin to fall at the same speed.
During the second leg of the drop, differences in the
falling speeds occur due to sedimentation - the coarser
particles fall at a higher speed than the finer particles.
The frequency spectrum of the backscattered microwave
signal contains information about the speed of the particles.
If speeds in the higher range are detected, this directly
indicates the presence of larger particles and thus quickly
alerts the operator to the possibility of a screen break.
- 1 x microwave particle sensor (reference sensor)
- 1 x microwave particle sensor (measuring sensor)
- C3-Box
- Transmitter in DIN Rail or field housing
- 2 x sensor socket for welding on the pipe
- Manual
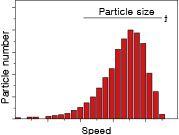
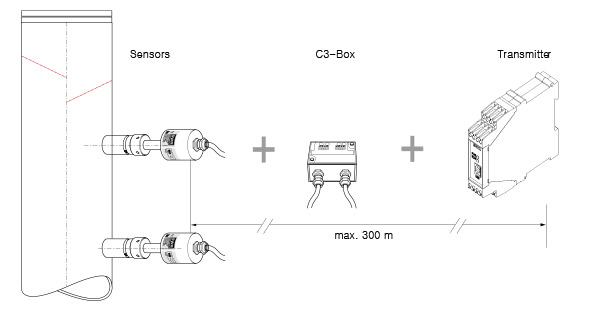
A PADDY measuring point necessarily requires two sensors and two baffle plates in the pipeline. The baffle plates ensure a controlled flow of material in front of the two sensors.
The positions of the baffle plates and the sensor mounts are determined by ENVEA - SWR engineering, as there may be differences from application to application.
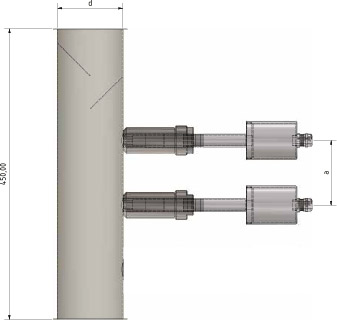
Measurement principle | Microwave |
---|---|
Measurement range | Particle sizes up to 10 mm - larger sizes on request |
Housing material | Stainless steel 1.4571 |
Protection type | IP 65, dust explosion zone 20 or gas explosion zone 1 (optional) |
Power supply | 24 V DC ±10 % |
---|---|
Power consumption | 20 W / 24 VA |
Protection type | IP 40 to EN 60 529 |
Ambient operating temperature | -10 … +45 °C |
Dimensions | 23 x 90 x 118 mm (W x H x D) |
Weight | Approx. 172 g |
DIN rail fastening | DIN 60715 TH35 |
Connection terminals cable cross-section | 0.2-2.5 mm2 [AWG 24-14] |
Current output | 1 x 4 … 20 mA (0 … 20 mA), load < 500 Ω |
Interface | ModBus RTU (RS 485) / USB |
Pulse output | Open Collector - max. 30 V, 20 mA |
Relay contact | Max. rated load: 250 V AC Max. peak current: 6 A Max. rated load 230 V AC: 250 VA Max. breaking capacity DC1: 3/110/220 V: 3/0.35/0.2 A Min. switching load: 500 mW (10 V / 5 mA) |
Data backup | Flash Memory |
Ambient operating temperature | Sensor tip: -20 … +80 °C Optional: -20 … +200 °C Sensor element: 0 … +60 °C |
Max. operating pressure | 1 bar |
Operating frequency | K band 24.125 GHz, ±100 MHz |
Transmission power | Max. 5 mW |
Weight | 1.3 kg |
Dimensions | Ø 60, Ø 20, L 271 mm |
Power supply | 110 / 230 V AC 50 Hz (optional 24 V DC) |
---|---|
Power consumption | 20 W / 24 VA |
Protection type | IP 65 to EN 60 52910.91 |
Ambient operating temperature | -10 … +45 °C |
Dimensions | 258 x 237 x 174 mm (W x H x D) |
Weight | Approx. 2.5 kg |
Interface | RS 485 (ModBus RTU) / USB |
Cable screw connectors | 3 x M20 (4.5 - 13 mm Ø) |
Connection terminals cable cross-section | 0.2 - 2.5 mm² [AWG 24-14] |
Current output | 3 x 4 … 20 mA (0 … 20 mA), load < 500 Ω |
Pulse output | Open Collector - max. 30 V, 20 mA |
Relay contact | Max. rated load: 250 V AC Max. peak current: 6 A Max. rated load 230 V AC: 250 VA Max. breaking capacity DC1: 3/110/220 V: 3/0.35/0.2 A Min. switching load: 500 mW (10 V / 5 mA) |
Data backup | Flash Memory |